Interview with artist Michael LeBlanc
Michael LeBlanc is a cast metal sculptor based in Northwest Arkansas. He offers foundry-based workshops and demonstrations in which he presents not only the process but also the history of cast metal arts. For over 15 years, he has been exhibiting and presenting research, both nationally and internationally, on cast metal art. In 2013, he was awarded the title of Mold Master by the National Conference of Contemporary Cast Iron Arts and Practices. More of Michael’s work can be found at Boswell Mourot Fine Art in Little Rock.
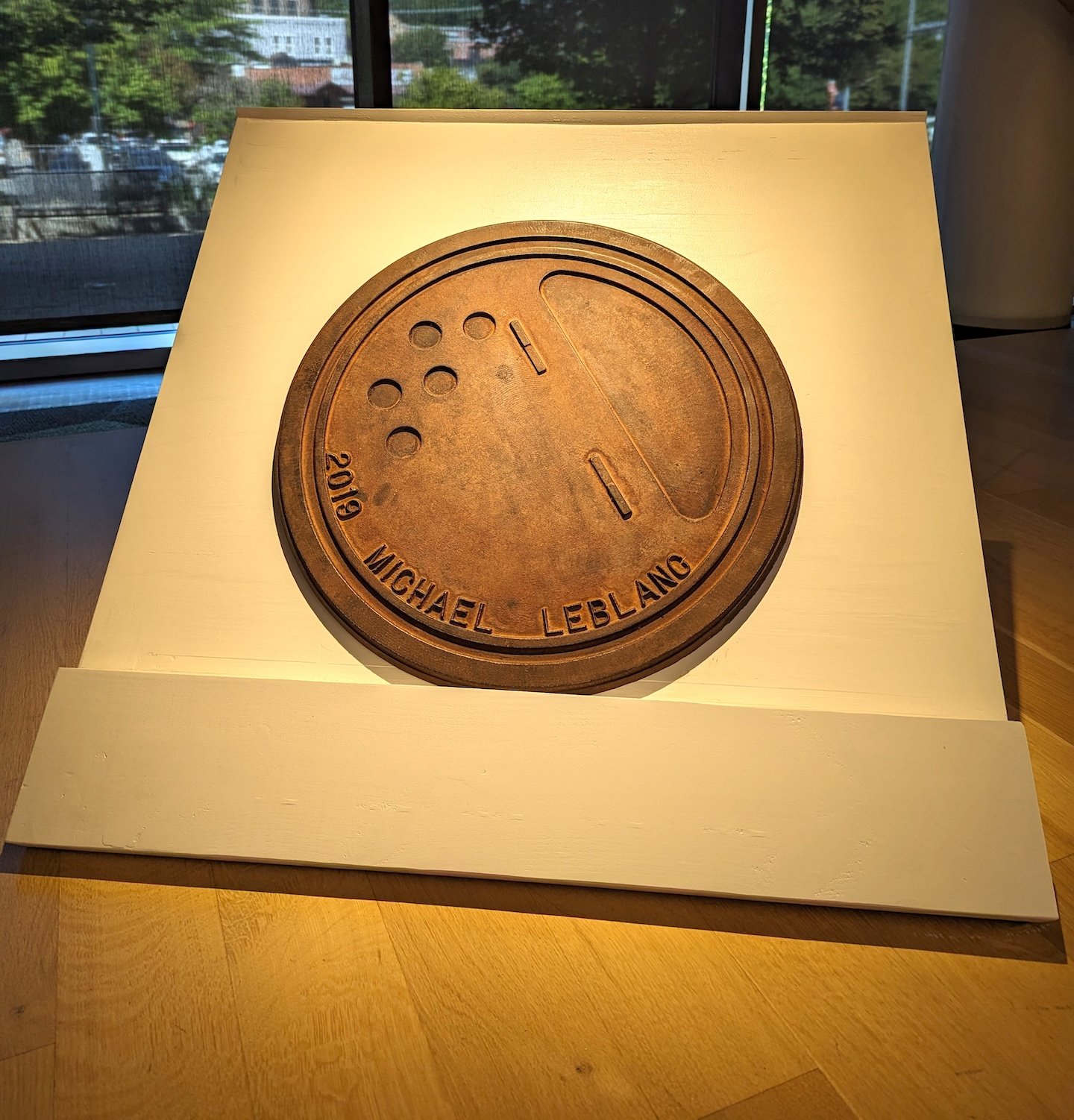
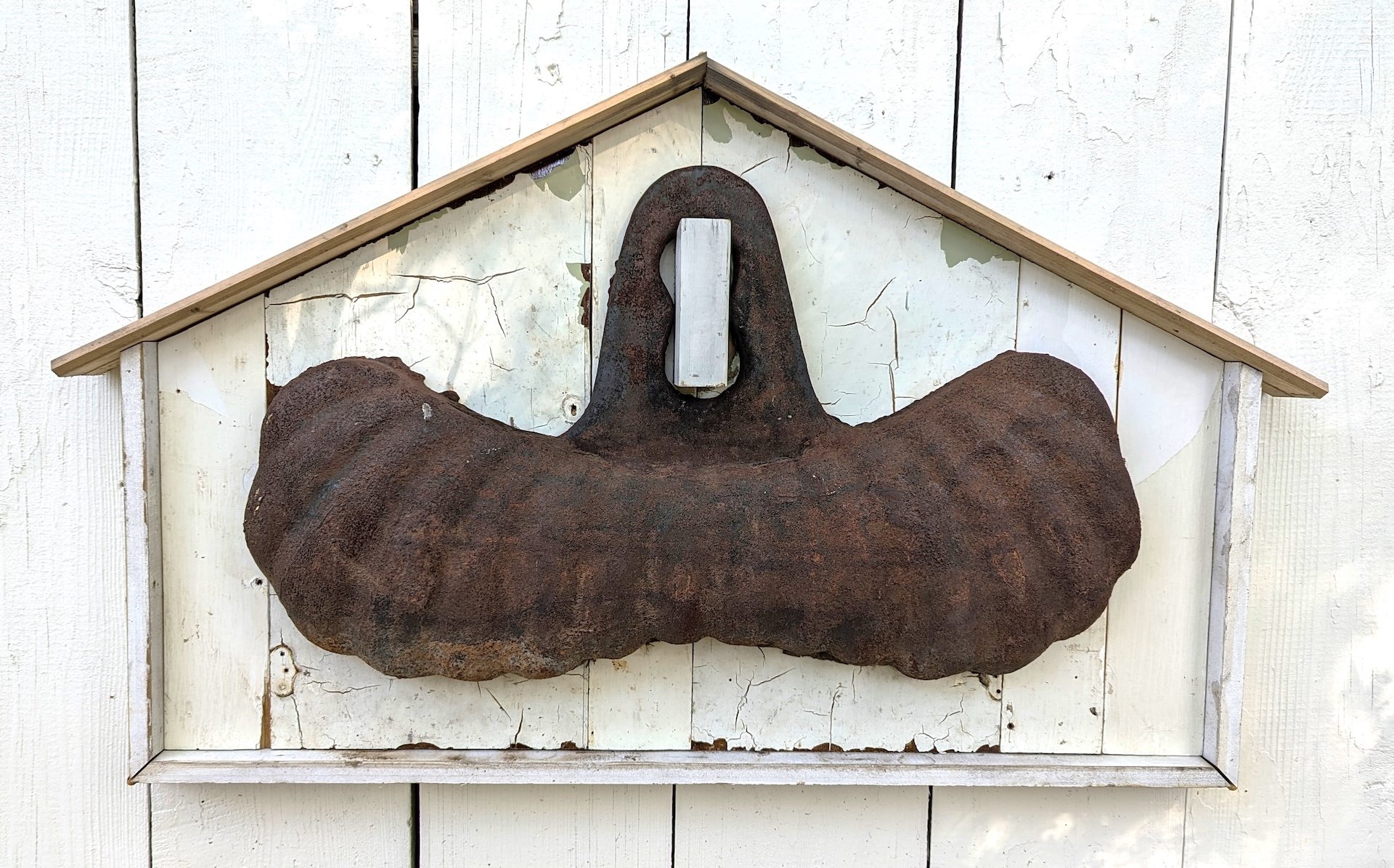
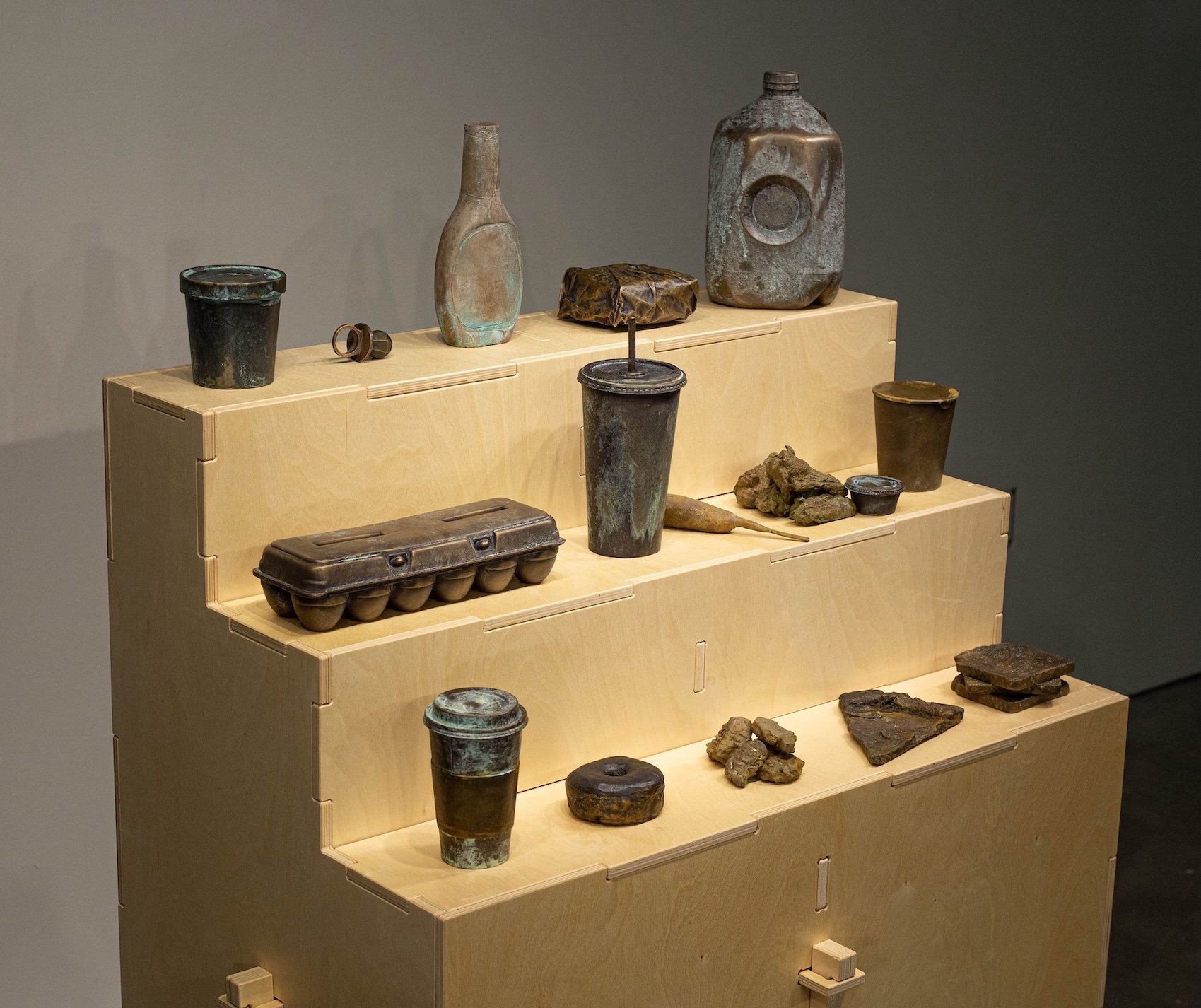
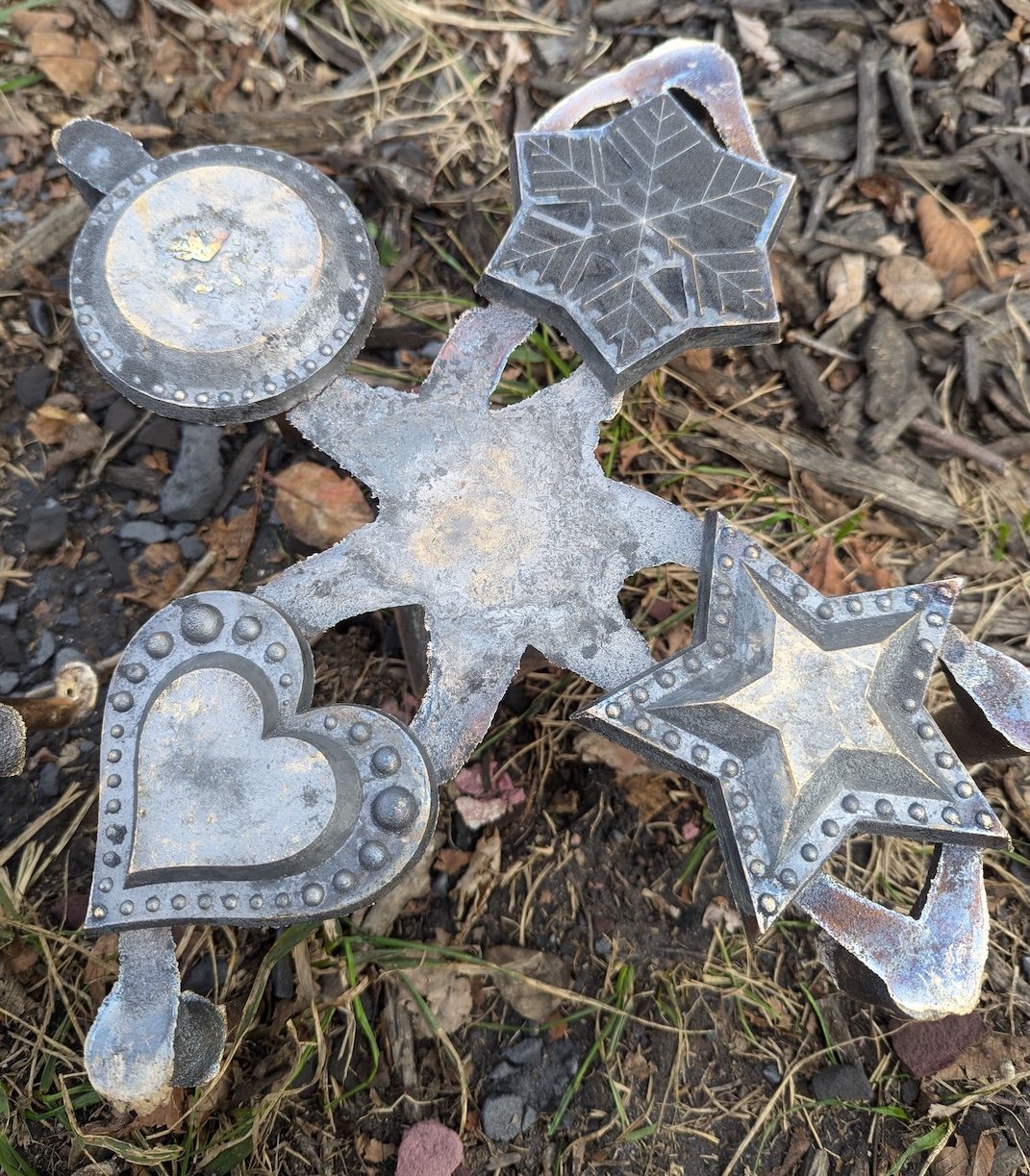
AAS: Michael, where are you from originally?
ML: I was born in Bloomington, Indiana but I am a “3rd generation out of the swamp” Cajun with ancestral ties to South Louisiana. Even though I never lived in South Louisiana, my family took trips to Lafayette almost every year in my youth to put flowers on my grandparents’ graves, visit my great aunt, and enjoy the food culture. We would take day trips to New Iberia to eat seafood and visit family at their boat landing.
I took five years between undergraduate and graduate school to discover what lifestyle and quality of life I could make for myself. I worked at a fine art bronze foundry in Atlanta, Georgia, a nonprofit art organization educating underserved communities in Portland, Maine, and had an artist residency at a cast iron historical site in Birmingham, Alabama. I considered graduate school and eventually accepted a full tuition waiver scholarship and graduate assistantship at the University of Arkansas in Fayetteville to earn my Master of Fine Arts in Sculpture. I graduated with my MFA in 2022, focusing on CNC advanced digital technologies and community engagement.
In the early to late 90’s I lived in Little Rock so it has been a full circle moment to live in Arkansas again and I enjoy living in Northwest Arkansas. I continue to find and be awarded artist opportunities to continue my professional practice. I have made lifelong friendships including marrying my wife last spring. I am slowly building my vision for my foundry and cast metal art practice through art exhibitions, workshops, and demonstrations for the public. I now live in Bentonville, Arkansas and am grateful for what Arkansas has provided for me and my career, and I am here to stay.
AAS: Did you have artist role models growing up?
ML: My artist role models started arising when I went to college at the University of West Georgia at Carrollton, Georgia in 2007. Role models were a variety of peer, professional, and teacher-based relationships. As a young adult, it was helpful to be exposed to so many different perspectives and to take aspects to these role models a la carte to start developing who I wanted to grow into and what my art would represent. These relationships have become lifelong friendships where we might not see or speak to each other in years and just pick back up where we ended last time.
AAS: When did you first become interested in sculpture and casting metal?
ML: I was not very interested in continuing my education after high school. My loving parents in their infinite wisdom knew that it was in my best interest to complete a college degree for my future self. They kindly drove me to the University of West Georgia, an hour south from our home in Rome, Georgia to start college in 2007. I struggled throughout my school career, especially in reading and writing so I chose to be an art major because I liked working with my hands. In my second semester, I participated in an iron pour that would change the course of my life. An iron pour is where artists throw refined coal and broken pieces of cast iron bathtubs into a cylindrical tower furnace reaching over 2,500°F and pour its molten metal into molds made of sand and resin to create art. It is a whole production where individual artists, wearing head to toe rawhide safety gear and hardhats with face shields, collaborate for a greater purpose. At the time, I did not know what art was, but I loved the idea of swinging a sledgehammer to break things and playing with a massive but controlled fireball. My poor mother probably had a heart attack after I told her what I was doing to pursue an art degree for the first time. After a certain amount of time though, the industrial process became secondary to the content I was interested in creating. Even further down the timeline, my reading and writing ability would be the major factor in being awarded grants to continue my cast metal and foundry practice. Nowadays, I am a grant writer for a cast iron art foundry and sculpture park. Funny how things pan out… Who tricked me?!
AAS: You studied in Japan a few years ago. What was that experience like?
ML: In 2019, I was awarded the Sturgis Fellowship from the Fulbright College of Arts and Sciences at the University of Arkansas at Fayetteville. I studied in Onishi, Japan, a small town of roughly 5,000 people for a semester. Onishi is about three hours by train north of Tokyo in Gunma prefecture. My research while abroad was to create artwork, study traditional Japanese artmaking in ceramics and cast iron, and societal practices in a community-based culture. It was a once in a lifetime experience, where your actions and inactions have profound consequences in the community. It was refreshing to experience this culture because I try to put intention and consideration in my actions. I made some lifelong friends where we exchange internationally mailed care packages with each other about once a year.
AAS: Of course, given my Cajun heritage, I must ask you about Okra/Legacy. That one would make one hell-of-a-big Cajun shrimp and okra gumbo. What is the process of creating such a cast metal sculpture?
Okra/Legacy, 28”x 48”x 28”, cast iron and wood
ML: Well, I prefer my father’s day after Thanksgiving turkey and sausage gumbo but all gumbo is good gumbo. For Okra/Legacy, I 3D scanned a piece of okra, scaled it up using 3D modeling software, CNC routed it in foam, molded the foam pattern using resin bonded sand in multiple pieces, poured the molds with molten iron, demold and rough cut the raw metal castings, weld the pieces together, fine sand and polish the casting, and chemical patination and wax seal the finished art. If there is a failure in the metal pouring stage, the entire process must be restarted. All the tools and equipment needed to melt, cut, or weld the metal castings are industrial graded or one off personally fabricated. When I select an icon to cast in metal, it is one of curated research and selection because of the lengthy creation process.
AAS: Tell me about your portable pedestals and display stands designed and built for your M.E.A.L.T. project.
M.E.A.L.T. Phase 1 (Pedestal Display), metal castings displayed on CNC baltic birch portable pedestals at the University of Arkansas.
ML: M.E.A.L.T. stands for Meet Everyone with Art at Location and Time. M.E.A.L.T. is a portmanteau of meal and melt referring to the food-based iconography and melting process of metal casting. Phase 1 of this project is a mobile museum of cast bronze artwork. The project was conceived in the height of COVID in 2021 as a way to engage communities safely while minimizing the spread of COVID. There is a logbook component of this project to record viewers' experiences to reflect that people might find commonality in fundamental aspects such as food. I designed and built the pedestals for this mobile museum using CNC technologies so I could easily deploy viewing events and transport and store them effectively. The pedestals are made of several pieces and fit together like a 3D puzzle where pins hold them together. I constructed two types of pedestals: one for single or couple item viewing and another for fully showcasing a collection of metal castings.
AAS: I really love that you choose to cast ordinary objects. Two of my favorites are the Starbucks Grande Latte and the chocolate donut. Could you explain your thought process regarding what objects you choose to elevate to Pop Art?
Starbucks Pumpkin Spiced Latte and Cronuts-Donuts Chocolate Glazed Donut both cast in bronze
ML: I make a considered effort in selecting iconography and curating content to reach a large and diverse viewer group while gently emphasizing community engagement and intertwined social values. For M.E.A.L.T. Phase 1, I was always thrilled when audiences from multiple age groups, ethnic backgrounds, and professions wrote in the logbook and discovered that they shared similar thoughts and experiences from different communities. When viewers unknowingly discover that they have similar responses from one another such as their personal importance or luxury of a Pumpkin Spiced Latte from Starbucks, I wonder what their next action will be. Are they more willing to start a dialogue with another viewer or next time in line waiting to order a coffee? Did that realization possibly challenge a preconceived notion, if even for a moment? Those are worthy pursuits and the crux of why to cast a novelty coffee in a historically important and regal medium such as bronze.
A colleague once coined my art practice as “Pop Art with a Heart.” That has a nice jingle and cadence that resonates with me. It is light, fun, possibly humorous, and yet intentional and empathetic. I would fall under the Pop Art category and enjoy Claes Oldenburg’s work very much. My favorite artist though is hands down Robert Arneson – playful, humorous, and yet critical and outspoken.
AAS: A large collection of your bronze work was accepted into the Arkansas Museum of Fine Arts’ Delta Triennial this past summer. What was that experience like?
M.E.A.L.T. Phase 1 (Cabinet Display), cast bronze and CNC baltic birch, 2024 Delta Triennial, Arkansas Museum of Fine Arts
ML: Being selected to exhibit at the Delta Triennial at the Arkansas Museum of Fine Arts in Little Rock was a career defining achievement. Around 1,200 regional artists applied to be showcased, but only 39 were accepted with several being extended an invitation. It was a humbling experience to be included, for even a brief time, alongside such pivotal art history defining artworks and artists. I have been practicing foundry and cast metal arts for 15 years, so it is pretty jaw dropping to be featured in such a prestigious venue for how short a time I have been practicing.
From that exhibition appearance, I was extended an artist contract to showcase and sell my artwork with Boswell Mourot Fine Art in Little Rock. In addition, I have been awarded multiple grants this year centered around my foundry practice. 2024 has been solidifying for my artistic career.
AAS: I really want to learn more about your community M.E.A.L.T. project. How did it develop and what are your goals for the project.
Michael pouring molten bronze into molds to produce a raw casting.
ML: During the COVID lockdown, around 2021, I discovered that there were no fine art foundries outside Arkansas's academic realm. M.E.A.L.T. was an artistic invention to advocate foundry-based arts and skill based learning. M.E.A.L.T. is a 3-phase project that can operate independently and cooperatively along with each other phase. Phase 1 is a mobile bronze fine art museum to bring the art viewing experience to communities. Phase 2 is a mobile fine art foundry offering workshops and demonstrations to the public. Phase 3 is a fine art foundry residency center and hub for creatives to learn about foundry and cast metal arts. Phases 1 and 2 are operational and active in the Northwest and Central Arkansas regions. Phase 3 is some time away, but it is important to have long term goals and rough draft out expectations for the future.
AAS: Congratulations on your recently awarded Arkansas Folk and Traditional Arts Mentorship Grant and Builders + Backers Idea Accelerator Grant. What will these opportunities do for you?
ML: For the Arkansas Folk and Traditional Arts Mentorship Grant, in the first half of 2025, I will be training my foundry assistant, Piper Hart, to become independent using the foundry so she can create a new collection of cast metal sculptures. Piper has been working with me for four years and I am grateful to have this time to concentrate on her wants and wishes creating cast metal sculptures. At the end of the mentorship, Piper and I will prepare an exhibition of the new artworks made during this period.
With the Builders + Backers Idea Accelerator Grant I received business and marketing acumen training at the end of 2024 as an arts entrepreneur using my fine art foundry. The experience was practical and educated me on how to set up a business model. Of course, creating and exhibiting the artwork are the most attractive parts of being an artist but being business savvy allows me to have an artistic career and future.
2024 has truly been a blessed year for my art career. I am grateful to be able to share so much of my art with the public and give a little back in 2025. I am looking forward to keeping the momentum going!
Michael probing a crucible of molten bronze with a pyrometer.
Piper Hart prepping molds for a bronze pour.
AAS: Michael, it seems you are having a lot of fun with your art? What can we expect next?
ML: Yes, I have a lot of fun with my art practice. My humor and lightheartedness flow into my creativity and community engagement, which circulate back into my purpose, intention, and thoroughness as a practicing artist. When the furnace is running and molten bronze is over 2,000°F though, it is time to work and ensure all safety measures are taken. Most foundry injuries, while infrequent, are severe relating to third degree burns to feet, hands, or face due to improper training and operations and lack of proper tools and equipment. I love having fun with my art while also being safe. My success in 2024 was in no small part due to the collaboration and tireless preparation of several people I would like to acknowledge over the recent years. Thank you, Vincent Edwards, Sam King, Piper Hart, Chris Schultz, Bryce Briscoe, Ashley Sutterfield (my ever-patient wife), and my family for your support, guidance, love, and friendship.
Rendering of a 3-foot diameter diamond to be cast in bronze.
2025 is already shaping up to be a great year for my art practice. My goal this year is to cast a 3-foot diameter brilliant cut round diamond in bronze. It will be a fun and lengthy sculpture to create. In the pursuit of highlighting icons that are touch points of commonality and shared interests for people, what is more relatable for Arkansans than the diamond? We have diamond icons littered over our government forms and licenses. We are the “Natural State” where residents and tourists dig for diamonds at the Crater of Diamonds State Park in Murfreesboro, Arkansas. It just seems… natural.